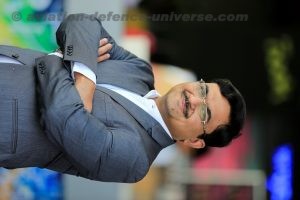
By Amit Agarwal, Director Technical – India, ASEAN and ANZ, Ansys
Bengaluru. 06 August 2021. For any industry to remain competitive, it needs to embrace exponential innovation and the transformations that come with it. The aerospace industry is at a phase where, pressured by new environmental and safety regulations, rising fuel costs and consumer price concerns, it is in dire need of innovative product solutions that can be delivered faster than ever. Breakthrough technologies are the need of the hour with many countries joining the space race and challenging the status quo. There is also the need to optimize maintenance, repair and overhaul as well as sustainment operations. There are also the emerging next generation autonomous and highly connected urban air mobility solutions. These overwhelming complexities have to be delivered without any compromise on safety.
Pervasive Simulation
Only 7% of A&D companies have fully integrated digital threads. Simulation solutions allow the creation of a digital thread from the program and product concept through development, manufacturing, testing, production, training, sustainment and acquisition that delivers innovative technology faster and at substantially lower cost. Simulation can thus help companies accelerate their digital transformation through comprehensive multidisciplinary solutions, an integrated and open platform, ecosystem, and skilled workforce.
Future designs benefit from past lessons
The “digital thread”, a cutting-edge concept is a common set of engineering and product performance data that is expanded daily and shared by all key stakeholders in the business. By making engines more digital and more connected over time, there is a generation of huge performance data. By using extensive analytics, combined with physical models enabled by advanced simulation capabilities, aviation companies can get meaningful insights that could be used to improve product performance and reliability, profitability, and customer-oriented solutions. It is optimized according to how engines actually operate and engineering simulation data plays a central role in this strategy.
Simulations of jet engine components and systems are numerically large and involves multiple physics, complex reactions and transient forces. Apart from its significant contribution to the speed, cost and quality of product development processes, simulation benefits would be amplified if all simulation data were collected and made accessible to all. Data can be gathered for each product design at the earliest stages of ideation and that data follows the design throughout its lifecycle, as the component is verified, tested, redesigned and released to the manufacturing function. Any design rework is simplified because all existing information related to that design is immediately available and unambiguously identified by the same part number. Costly and time-consuming repetitive handoffs can be eliminated. Anyone, anywhere in the business can see at a glance where each design stands and easily contribute to the product’s ultimate success.
The result of digitized product development process is a virtual prototype produced through collaborative engineering and is ready for physical testing. Any physical test results are collected as part of the digital thread, impacting any rework on that product, but also becoming part of the company’s general knowledge base.
Digital Twin
Digital twins will close the loop on the digital thread and create a view of a product design’s entire lifecycle, from earliest ideation through real-world operation. The insights gathered will be available to every stakeholder, impacting future designs and forming the footing for high product performance for the future.
Electrification
Roughly 5% of scheduled airline flights worldwide fly 100 miles or less. For this, a turbine/piston aircraft consumes about $400 in fuel and release CO2 and other greenhouse gases. An electrically propelled plane could make that same trip using $12 worth of electricity, producing no tailpipe pollutants and be quieter.
Electrification is a powerful driving force in most industries, but until recent times, aircraft propulsion wasn’t one of them. Some components of aircrafts have been made more electric now like power generation management, passenger comfort, air pressurization, air conditioning and flight control but a good electric propulsion aircraft hasn’t emerged because there has not been an electric propulsion system powerful enough and light enough to power an aircraft. Though electric planes have been on people’s mind for a while, the technology’s not quite ready and that’s where simulation can help. Structural, electromagnetic and thermal simulation solutions can be used to design and test the robust, reliable electric motors needed to ensure aircraft safety and reliability and bring electric-powered airplanes to the market faster.
Challenges of an Electrically Propelled Aircraft
In an aircraft, reducing weight while maintaining the mechanical strength and performance of the motor and other components is critical as is optimizing the electromagnetic properties of the motor to provide the most power possible in a small, lightweight package.
Multiphysics simulations can be performed to optimize structural integrity, fluid flow and the electromagnetic properties of innovative electric motors in order to meet these design challenges. The electromagnetic behaviour of the motor can be analysed and optimized for weight using simulation. Simulation data from the electromagnetic analyses, such as losses and internal forces can be shared to perform thermal and structural multiphysics simulations. Structural components of motors can be analysed to ensure that they are robust and lightweight given all loading conditions.
Lighting up is one of the most important trends in the aerospace industry as jet manufacturers and their suppliers work to reduce the overall weight of planes to improve their fuel efficiency. Simulation helps in making aerospace lighter and smaller with additive manufacturing. A defense industry start-up applied our simulation, high performance computing and 3D printing technology to deliver order of magnitude reductions in size, weight and development time for a SATCOM- integrated array antenna. When it comes to lightweighting an airframe, using our composite material solutions enabled engineers to reduce modeling time by up to 65% over traditional solid modeling.
Simulation solutions also help study both air and coolant flow in and around the motor to understand how the motor will behave thermally in service. Engineers can even determine the effects of one modification to the system like a change in the electromagnetic design, on the other physics involved, like the mechanical and thermal properties. Given the combined thermal and structural loads on the motor, engineers can determine maximum stresses and displacements, and then study the design to see what areas may need optimization. After deciding what area to focus on to improve the design, they can modify the inputs to the relevant solver and run another multiphysics iteration.
Cost Reduction and Accelerated Innovation with Simulation
With Ansys simulation, the aviation industry is able to realize dramatic cost reductions across the entire product lifecycle while simultaneously delivering innovative technology that will shape the future of the industry. In A & D, simulation has already proven to reduce acquisition cycle time by 20%, acquisition labour efficiency improvement by 30% and maintenance cycle improvements by 30%. With simulation, a product is 58% more likely to meet cost targets. Also, simulation makes it 44% more likely to keep up with product launch date. There is a 36% reduction in safety test cycles and 28% reduction in additive manufacturing prototypes. Simulation addresses safety, sustainability and affordability. Thanks to simulation, for A & D, we have managed to achieve 25% more fuel efficiency per seat, lessen noise by 75%, extend service life by 10 years and also managed a 40% increase in maintenance interval for aircrafts. That’s not all, simulation can cut down safety certification time by half. Engineers can predict the performance of proposed installations without the time and expense of building prototypes.
Be it Aerodynamics, Airframe, Aeroelasticity, Avionics and Flight Controls or Communication & Electronics, simulation has proven its worth. Be it product lifecycle cost reduction, safe and sustainable aviation, predictive maintenance, future aircraft systems and urban air mobility, simulation is the answer that you’re looking for.